Hoist Loaded FIBC Discharging into High Shear Mixer
Discharging powders from Flexible Intermediate Bulk Containers (FIBCs) into a high-shear mixing line offers several benefits in industrial processes. Here's a breakdown of these advantages:
1. Improved Efficiency in Material Handling
Bulk Processing: FIBCs allow for the transportation and handling of large quantities of powder at once, reducing the need for frequent refills and improving throughput.
Automated Systems: Many setups integrate automated discharging equipment for FIBCs, minimising manual intervention and speeding up the feeding process into the high-shear mixer.
2. Enhanced Mixing Quality
Uniform Feeding: FIBCs provide a consistent and controlled flow of powders, ensuring steady feeding into the high-shear mixer. This uniform input helps achieve homogeneous mixing and prevents localised over-saturation or dry spots in the mix.
Prevention of Agglomeration: High-shear mixers rely on consistent input to efficiently break down agglomerates and achieve fine dispersion. Big bag discharging systems are designed to prevent clumping and ensure free-flowing material. Sieves, Sifters and Nibblers can be incorporated to achieve various levels of size reduction.
3. Reduced Dust and Contamination
Enclosed Systems: When combined with dust-tight spouts or specialised discharge stations, FIBCs significantly reduce dust generation during powder transfer, improving workplace safety and reducing material loss.
Hygienic Operation: In industries such as food, pharmaceuticals, and chemicals, closed systems minimise contamination risks, ensuring compliance with hygiene standards.
4. Cost Savings
Reduced Labor Costs: Automated or semi-automated systems for discharging FIBCs reduce manual labor compared to handling smaller containers or bags.
Lower Packaging Costs: FIBCs can replace multiple smaller containers, lowering the cost of packaging materials.
5. Versatility in Handling Various Powders
FIBCs are compatible with a wide range of powder types, including fine powders, granules, and hygroscopic materials. Many systems incorporate flow aids such as vibration or aeration to handle powders prone to bridging or rat-holing.
6. Increased Safety
Dust Control: By minimizing airborne dust, FIBC discharge systems reduce risks of explosions in industries handling combustible powders.
Ergonomic Advantages: Automated or gravity-fed FIBC systems reduce the physical strain on workers compared to handling heavy bags manually.
7. Time-Saving in Downstream Processes
Direct Feeding: FIBC discharging stations are often integrated directly into the high-shear mixer line, streamlining operations by eliminating intermediate steps such as batch weighing or transferring materials from smaller containers.
Continuous Processing: For setups with continuous high-shear mixing, controlled FIBC discharge ensures the process runs without interruption.
8. Scalability and Adaptability
FIBC systems can be scaled easily to meet varying production needs, whether for small-scale batches or large industrial operations.
Discharge stations can often be equipped with features like load cells, vacuum conveying systems, or screw feeders to accommodate different plant configurations.
9. Improved Environmental Impact
By reducing waste (less spillage and fewer single-use bags), FIBC systems contribute to more sustainable operations.
Dust control measures also help ensure compliance with environmental regulations.
Summary
Discharging powders from FIBCs into high-shear mixer lines combines the logistical advantages of bulk handling with the operational precision required for high-quality mixing. The result is a system that enhances efficiency, safety, and product consistency while lowering operational costs and environmental impact.
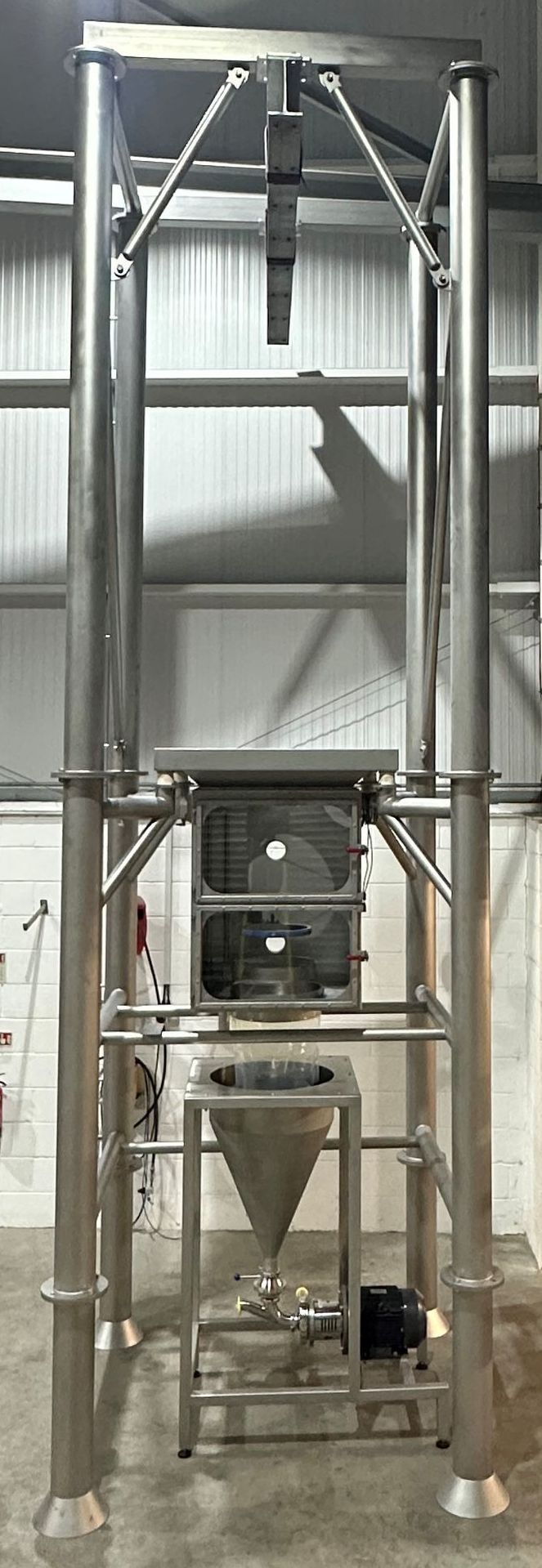