Benefits of Using Dust-Tight Seals and Containment When Discharging Powders from FIBC's
In industries such as food, pharmaceuticals, chemicals, and manufacturing, the handling and discharge of powders from Flexible Intermediate Bulk Containers (FIBCs) require meticulous control to maintain product quality, protect workers, and ensure compliance with regulations. One of the most effective ways to achieve this is by using dust-tight seals and containment systems during the discharge process.
Here, we explore why dust-tight seals and containment are essential and the key benefits they bring to industrial operations.
1. Improved Dust Control for Safety and Cleanliness
Powder discharge processes can produce airborne dust, particularly when fine or dry materials are involved. Uncontrolled dust can lead to workplace hazards and operational inefficiencies. Dust-tight systems help:
Maintain Clean Workspaces: Containment systems prevent dust from settling on machinery, floors, and other surfaces, reducing the need for frequent cleaning and maintenance.
Protect Worker Health: Airborne dust can cause respiratory issues or allergic reactions. Dust-tight seals ensure a safer environment by minimising worker exposure to hazardous particulates.
Reduce Fire and Explosion Risks: Fine powders, especially combustible ones, can create explosive atmospheres if dust is not properly contained. Sealing systems mitigate this risk.
2. Enhanced Product Quality and Integrity
Dust-tight seals and containment systems preserve the integrity of the powders being discharged. This is particularly important in industries with strict quality requirements, such as food and pharmaceuticals. The benefits include:
Prevention of Contamination: Sealed systems ensure that external contaminants, such as moisture, dirt, or foreign particles, do not mix with the product during discharge.
Consistent Material Flow: Containment systems often include features to prevent bridging and rat-holing, ensuring a smooth, uninterrupted flow of material.
Preservation of Product Properties: Proper containment prevents exposure to environmental factors that might degrade sensitive powders, such as humidity or air.
3. Regulatory Compliance
Many industries are subject to strict regulations regarding workplace safety, environmental protection, and product hygiene. Dust-tight systems play a key role in meeting these standards:
Health and Safety Standards: Adhering to regulations such as COSHH (Control of Substances Hazardous to Health) in the UK or OSHA (Occupational Safety and Health Administration) in the US often requires robust dust control measures.
Environmental Regulations: Minimising dust emissions helps facilities comply with environmental laws and reduces their impact on surrounding areas.
4. Operational Efficiency and Cost Savings
Dust-tight seals and containment systems streamline the discharge process, delivering long-term cost and operational benefits:
Reduced Downtime: By preventing powder spillage and contamination, facilities spend less time on cleanup and equipment maintenance.
Material Savings: Containment systems minimise product loss due to spills or dust dispersal, improving material efficiency.
Energy Efficiency: In closed systems, less energy is needed for ventilation and dust collection.
5. Worker Satisfaction and Safety
A clean, dust-free environment not only complies with safety standards but also boosts worker morale and productivity:
Ergonomic Discharge Processes: Modern containment systems often integrate user-friendly designs that reduce physical strain on operators.
Improved Visibility: By minimising dust clouds, workers can operate machinery and monitor processes more effectively.
6. Sustainability and Environmental Benefits
Dust-tight systems support sustainable operations by reducing waste and environmental impact:
Waste Reduction: Less material is lost during discharge, improving overall resource efficiency.
Lower Carbon Footprint: Efficient dust containment reduces the need for extensive cleanup efforts and energy-intensive ventilation systems.
Key Components of Dust-Tight Systems
To achieve the benefits above, modern dust-tight systems often include features such as:
Sealed Spouts: These ensure a secure connection between the FIBC and the discharge station.
Integrated Dust Collection Units: These capture any escaped dust before it enters the environment.
Clamping Mechanisms: These secure the FIBC during discharge, creating a fully enclosed system.
Anti-bridging Devices: These ensure consistent material flow, even for challenging powders.
Conclusion
Using dust-tight seals and containment systems when discharging powders from FIBCs is more than just a best practice—it is a necessity for safe, efficient, and compliant operations. By controlling dust emissions, protecting product quality, and enhancing workplace safety, these systems deliver measurable benefits across the board.
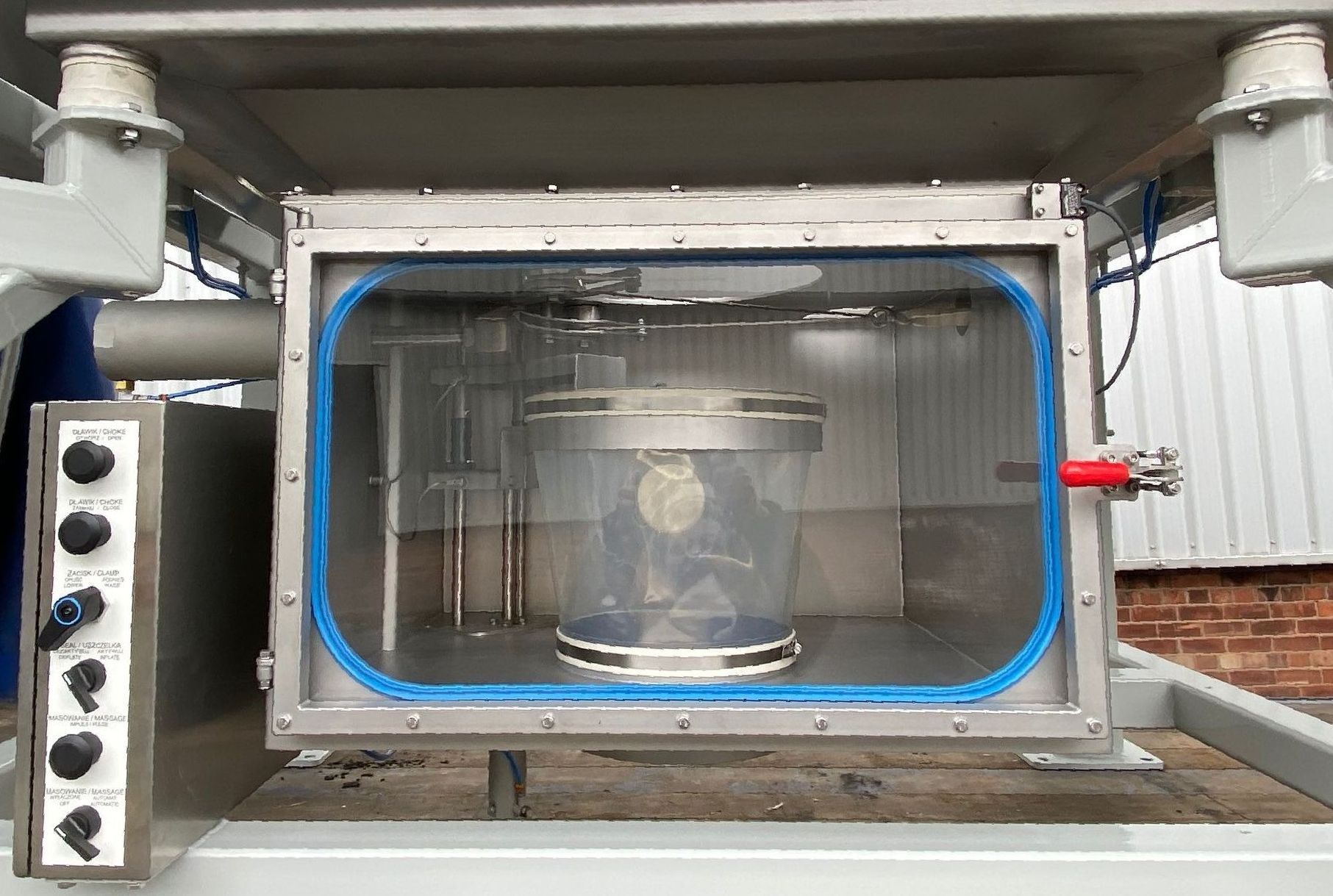
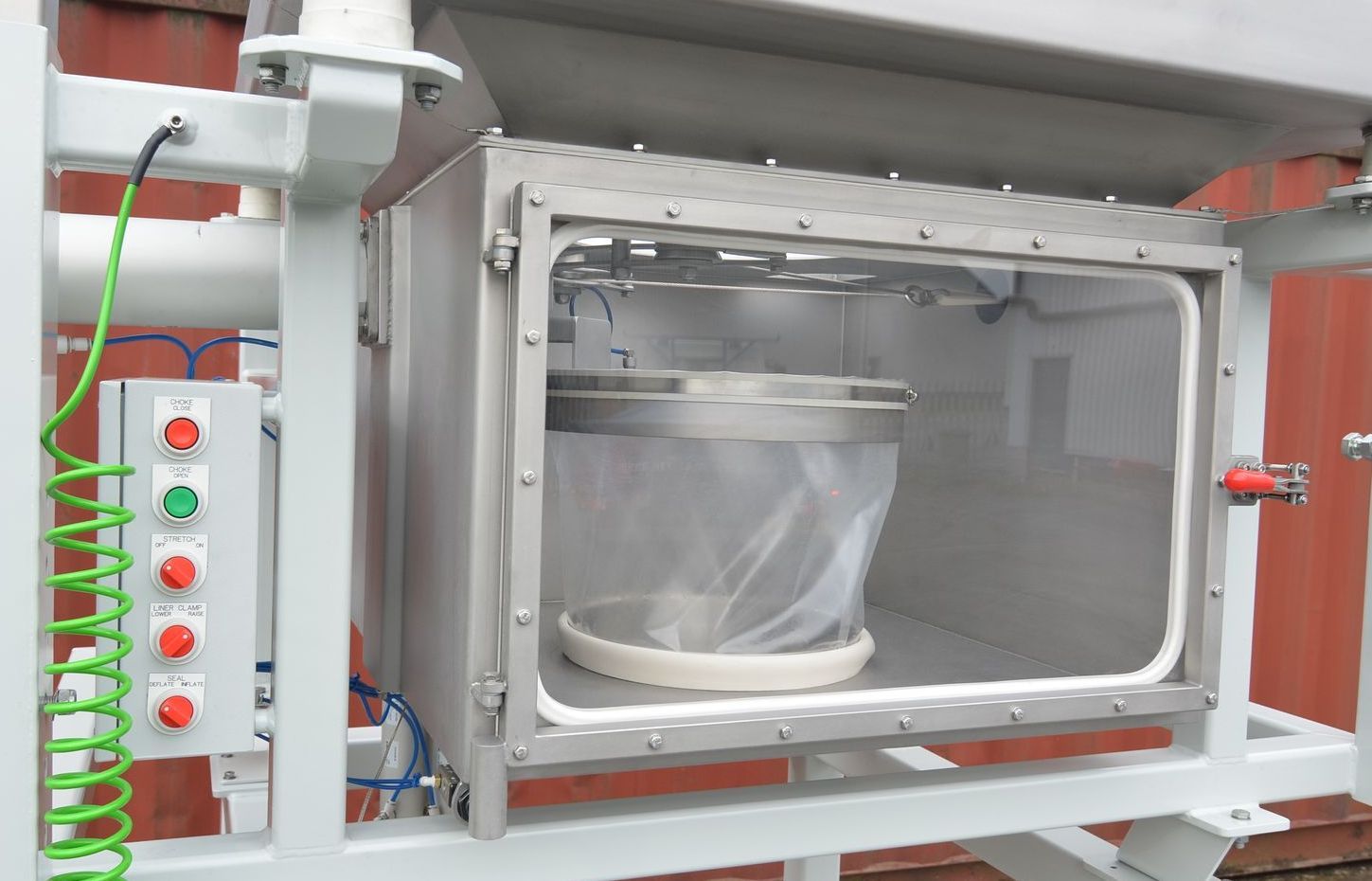